在制药行业中,片剂是最为广泛使用的剂型之一。片剂的生产过程包括原料药预处理、剂量分配、制粒、压片、包衣等多个环节,其中制粒工艺在整个片剂生产中扮演着至关重要的角色。流化床制粒作为一种高效、集成化的制粒技术,因其在混合、制粒和干燥过程中的优势,已成为制药企业优化生产流程、提高产品质量的重要选择。
一、力度干燥制粒在片剂生产中的重要性
片剂是由原料药和适当的辅料(如填充剂、吸附剂、粘合剂、润滑剂、崩解剂等)通过特定的制剂技术制成的固体制剂。在片剂生产中,制粒工艺是防止压片过程中可能出现的问题(如裂片、粘冲、颗粒不均匀等)并确保药品质量的关键环节。例如,如果制粒过程中粘合剂用量不足,颗粒过于干燥,可能导致压片时裂片;而颗粒过于潮湿则会导致粘冲、颗粒不均匀等问题。因此,掌握制粒工艺的关键要点对于药品开发者而言至关重要。
二、力度干燥制药生产中的不同粉末制粒技术
力度干燥在制药生产中,粉末制粒技术主要包括以下几类:
湿法制粒:通过加入粘合剂使物料形成湿颗粒,随后进行干燥。常用的设备是高剪切制粒机。
干法制粒:适用于热敏感材料,通过压片机将物料压成薄片,再破碎成颗粒。
流化床制粒:在流化床中实现物料的流化、粘合剂的雾化以及干燥,最终完成制粒。常用的设备是流化床制粒机。
喷雾制粒:将物料和粘合剂混合成溶液后进行喷雾干燥。常用的设备是喷雾制粒机。
三、流化床制粒工艺详解
流化床制粒是一种将混合、制粒和干燥等多个过程集中在流化床喷雾制粒机中完成的高效制粒技术。其原理大致如下:将原料和辅料加入封闭的流化床中,通过流化实现粉末的混合。在雾化压力和喷射速度的条件下,喷枪将液体喷入原料粉末中,使雾化的液滴围绕颗粒核聚集。随着液体的不断注入,颗粒核表面形成液桥,颗粒逐渐长大。液体桥中的水分蒸发后形成固体桥,最终得到多孔且呈圆形的颗粒。随着液体饱和度的增加,颗粒尺寸逐渐增大,孔隙率进一步降低。这就是流化床喷雾制粒机的工作原理。
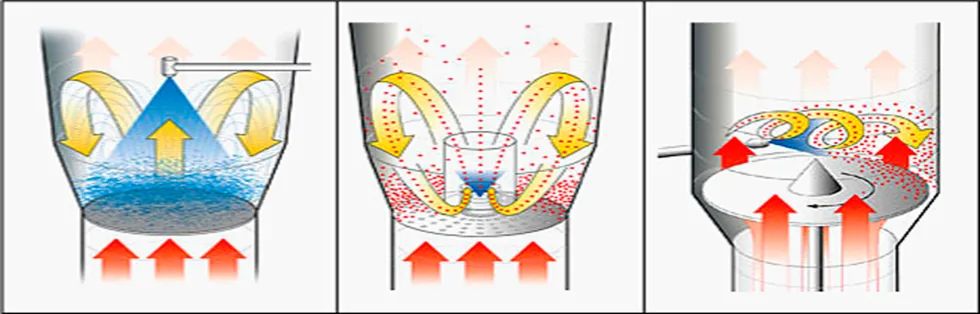
四、流化床制粒设备的组成与优势
流化床设备主要由以下部分组成:除湿系统(可选)、初效过滤器、中效过滤器、高温高效过滤器(H13)、准确控温的加热器、底部料斗、带小车的可移动产品容器、流化室、滤室、喷雾系统和排气系统。其结构从上到下可分为三个部分:最上部的圆柱体通常安装有滤袋,主要用于振动除尘;中部为圆柱形腔室,物料在上升气流和向下重力的作用下在料斗和腔室之间往返运动,颗粒悬浮在热干空气中形成良好的流化状态;
流化床一步制粒具有诸多优势,例如在流化床设备中完成物料的混合、制粒和干燥,减少了大量操作环节,节省了生产时间;在合适的工艺参数范围内,可得到粒度均匀、圆形、流动性好、可压性好的颗粒;设备封闭,有效避免了细粉飞扬,不仅防止了药品的外部污染,还减少了操作人员与刺激性辅料的接触,更符合GMP要求;高度自动化,易于放大和复制。
五、流化床制粒的关键参数选择
进风温度
流化床制粒的进风温度应根据物料的性质和所需颗粒大小进行控制。如果粘合剂的溶剂是乙醇等有机溶剂,进风温度应略低于水等溶剂。在其他参数不变的情况下,如果进风温度过高,会导致喷雾的粘合剂液滴过早干燥和蒸发,降低物料的润湿性和渗透性,影响颗粒的聚集能力,形成较小的颗粒。此外,过高的温度可能会使一些热敏感材料的性质发生变化。进风温度过低则会导致粉末过度湿润,部分物料粉末会相互聚集并粘附在容器壁上,无法保持良好的流化状态,更容易导致流化失败。具体温度设置需根据不同物料和工艺进行调整。进风速度
流化床一步制粒技术中,进风速度的选择基于流化床颗粒始终处于良好的流化状态。良好的流化状态主要取决于物料的水分和重量。在流化床一步制粒过程中,物料状态从干粉变为湿颗粒,再变为干颗粒,风机速度需要不断调整,通过变频器控制速度以确保良好的制粒状态。当浆料制粒时,随着颗粒湿度的逐渐增加,可以适当提高风机频率;合适的风量可以使物料处于良好的流化状态,热交换处于平衡状态,有利于制粒。如果风速过大,物料可能会被吹到滤袋上,单位时间内通过的热气流过多,导致粘合剂水分挥发过快,粘合力减弱,同时粘合剂液滴无法与物料充分接触,导致颗粒大小分布较宽,细粉较多;随着风速的增加,颗粒受到的冲击力过大,导致颗粒磨损过多。喷雾压力
喷雾液体压力是影响制粒质量的一个不可忽视的因素。喷雾压力是通过气流将粘合剂高度分散成雾化液滴的过程。一般来说,喷雾压力与最终颗粒大小呈反比关系。喷雾压力越大,雾化液滴越小,液滴的比表面积越大,热空气蒸发水分的速度越快,颗粒尺寸越小;反之,喷雾压力越小,形成的液滴越大,液滴更容易形成较大的颗粒团,润湿粉末的能力进一步降低。因此,应根据物料和仪器性能选择合适的雾化压力。喷雾喷嘴的压力通过控制柜调节压缩空气压力来调整喷雾压力。喷雾速率
喷雾速率的选择也与颗粒大小直接相关。喷雾速率与颗粒大小成正比,在一定的喷雾压力下,随着喷雾速度的增加,粘合剂的雾化液滴尺寸也会增大。如果流速过高,会导致机器内湿度过高,湿颗粒表面的水分无法及时干燥,可能导致聚集或粘附成团,颗粒尺寸增大,严重时可能导致流化床塌陷;反之,当流速过低时,颗粒尺寸可能会进一步减小,细粉过多,运行一段时间后也可能导致喷枪堵塞,大大限制了效率。文献研究表明,在喷雾压力和进风温度/物料温度保持不变的情况下,喷雾速率为10 mL/min时,颗粒合格率高。
综上所述,影响颗粒大小的因素包括进风量、进风温度、喷雾液体压力、喷雾速率和粘合剂浓度等。在制粒过程中,应结合实际的制粒情况,综合调整这些影响因素,以将颗粒大小控制在适当的范围内。
六、力度干燥提高流化床制粒质量的方法
控制风量
调整进风量,使容器内的物料充分沸腾并混合均匀,且沸腾层不超过喷枪。流化床干粒机的初始进风量不宜过大,否则粉末会沸腾过高并粘附在滤袋表面,导致气流受阻。调整风量时,进风量应略大于排风量。一般情况下,风量确定后,只需调整排风量以达到合适的沸腾状态。启动风机时,需先关闭风门,待风机运行后,逐渐增大排风风门,以形成理想的物料沸腾状态。控制进风温度
流化床制粒的进风温度过高会使颗粒尺寸减小,过低则会使物料过度湿润并形成团聚。因此,在沸腾制粒过程中,控制温度至关重要。蒸汽进入加热器,使空气在通过时被加热。由于蒸汽加热时温度会在一定时间内上升和下降,因此在设置和调整时需要注意提前控制和预测。个人经验表明,在使用生产设备时,蒸汽加热过程中存在约10°C的缓冲区,即设定温度为60°C时,温度可能上升至70°C,然后逐渐下降并稳定在60°C。因此,在制粒过程中调整温度时,需要提前关闭进风,或将温度设定为比理想温度低约10°C,待其相对平衡后再进行调整。控制喷雾液体速度
当温度达到要求后,即可进行喷雾制粒。此时需控制压缩空气的流量和压力以及粘合剂的流量和流速。同时,需开启滤袋的反吹(吹扫)功能,每隔几秒进行一次吹扫。床压波动一般应控制在±3%以内。如果压力波动超过±10%,流化可能不理想。压缩空气的流量和压力以及粘合剂的流量和流速需要适当,以确保产品的颗粒大小分布合适。防止粘附或沉降
在喷雾过程中,物料温度和排风温度会下降。当它们降至某一值时,需停止喷雾以防止壁粘附或沉降。当物料温度恢复至原始值时,再次开始喷雾,并重复此循环,直至粘合剂喷完。需注意不同粘合剂的最大粘度温度,并根据产品需求调整物料温度在最大粘度温度下的停留时间。防止结块
在喷雾室内,物料受气流和容器形状的影响,在中心向周围进行上下循环运动。粘合剂从喷枪喷出,粉末被粘合剂液滴粘附并聚集成颗粒,随后被加热。气流带走水分,需控制出口温度的变化。湿颗粒容易粘附在一起形成结块。其他导致结块的原因包括:装载量过多,需确保装载量适当;颗粒过于潮湿,需降低颗粒的水分含量;若存在死体积,可先干燥部分物料,再加入剩余的湿颗粒,或通过振动使颗粒松动。装载粉末量
装载量应适中,不可过多或过少。一般情况下,流化床制粒机的容器装载量约为其容器体积的60%-80%。过多或过少都会影响沸腾状态和制粒效果。消除静电
流化床制粒机的容器通常配备有静电消除装置,可及时消除粉末摩擦产生的静电。部分制造商为静电消除装置配备了单独的探头,使用时需手动插入,使用过程中需注意,切勿遗漏。静电是导致细粉吸附在收集袋上、影响压差、流化状态以及制粒不均匀的主要原因。沸腾状态不佳
收集袋长时间未振动,导致粉末吸附过多;沸腾高度过高,状态过于剧烈,床负压过高,粉末吸附在收集袋上。风道堵塞,进风和排风不畅。